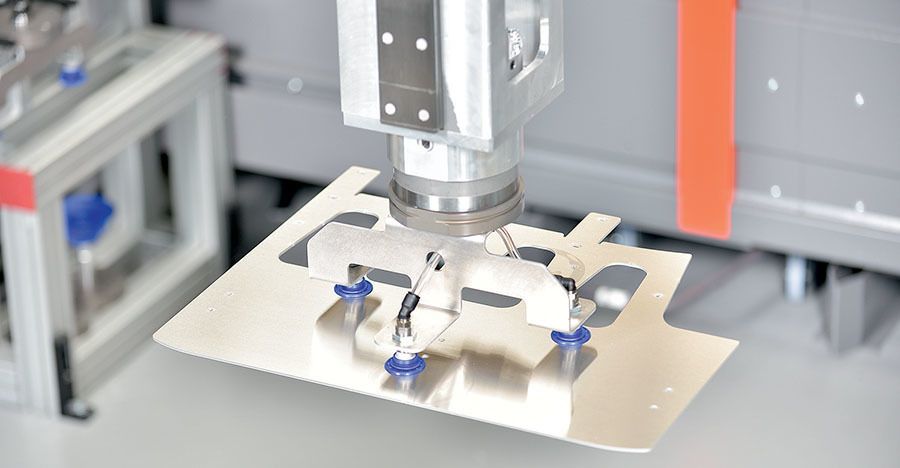
News Zen and the art of part flow maintenance
An end effector grasps a blank and carries it to the appropriate pallet. Programmers can plan to ensure robust stacking, cutting reliefs to ensure consistent part removal from the skeleton, perhaps even microtabbing small parts together into one "mini-nest."
Years from now, technical historians and industry lifers will reminisce about the days of yore. Not much more than a decade ago, CO2 lasers were state of the art and life in a metal shop was much simpler—well before we figured out how to cope with what a high-powered fiber laser was capable of. Some manufacturers are just now "settling in" with 10-kW-plus fiber lasers, and they’re doing it in ways that often surprise those industry lifers.
The 10-kW fiber laser, which emerged onto the scene seven years ago, set a paradigm shift that’s still in motion. With that incredible leap in laser cutting performance, the industry collectively stepped into the post-inches-per-minute (IPM) world, where cutting speeds could become irrelevant to the overall productivity of a business. The industry turned its attention from cutting speed to part flow velocity and overall throughput. Put another way, what goes onto a laser table must also come off.
The Holy Trinity of Productivity
The CO2 laser was an incredibly capable tool and, in the typical shop, drove a lot of the decision-making. It could cut any geometry with good speed, without the punch tooling limitations for sheet metal and at a fraction of the cost of waterjet consumables for thicker stock. This capability came at a cost, though. Being the apex of productivity, lasers were also the most expensive machines in many shops.
Then came the fiber laser, and fabricators raced to catch up with their productivity, first at 6 kW and then at 10 kW of cutting power. They were now too productive and incompatible with the culture of a shop accustomed to working with CO2 lasers.
Three KPIs of a CO2 laser department were a kind of holy trinity: Thou shall not deviate from optimizing (1) sheet yield percentage, (2) nest run-time, and (3) beam-on time. If fabricators kept those three metrics at or near their target level, a profitable and dare I say lucrative business could be had.
The industry has placed so much historical focus on these three KPIs, and it led to some challenges as fiber laser technology pushed relentlessly forward. A fabricator following the holy trinity of laser management could experience problems when upgrading to their first high-powered fiber laser—say, moving from a 4-kW CO2 to a 12-kW fiber laser machine.
Sheet Yield
Focusing on this KPI starts innocently enough, with the very real concept that time is money, but steel is also money (an increasingly variable amount of money lately).
Nesting software gives programmers a great amount of control. They can cut corners, skirt generally accepted rules, and common-cut parts they probably shouldn’t. Suddenly, a nest optimized for sheet yield alone presents problems in the machine. Nozzle collisions abound, and recovery times associated with interventions explode. Thus, for the first time, we enter the "conflict zone," where a laser operator and a programmer disagree on how the machine should be put to use.
Of the three KPIs in the holy trinity, yield is possibly the least affected by the high-power fiber laser. Part geometry is part geometry and material is material, after all. Still, the effect exists and can’t be ignored.
Nest Run-Time
This is actually the least important metric to care about in a high-power fiber laser environment. The biggest fallacy here is that if the new laser can achieve a feed rate five times faster than the old one, I as a shop owner should be able to achieve five times the output. That stands out on an Excel spreadsheet. The time studies look quite attractive, and the board of directors will certainly be convinced they’ll achieve a reasonable return on investment. It all sounds like a no-brainer proposition.
Imagine you’re a laser department manager whose employer is three months into owning a fiber laser—and your output is not exactly five times what it was previously. Are you in trouble? Probably not, because the rest of the shop is struggling to adjust for your new output. Management also may be struggling to understand why there’s so much laser-cut work in process (WIP) sitting around costing money in storage and net working capital.
Forget about all the machining sequence changing, pingponging, and common-cutting cheat codes you learned in the past because the laser was the lifeblood of the shop and needed to run as much as possible. You can avoid the "conflict zone" quite easily here. The new laser can satisfy your shop with literally zero effort in optimizing for nest run-time. Use the factory parameters or tech tables, a reliable cutting strategy, and you’re always a hero. What a life in the post-IPM world!
Beam-On Time
In the not-so-distant past, I walked a couple representatives from a prospective customer into an existing customer’s laser department, with the former wanting to look at a high-powered machine that the latter had installed a few months previously. We had really done our jobs as salespeople, telling the prospects that this would be an impactful visit. When we arrived, our host was very gracious and promised to answer any questions about the equipment. We let the customer lead the group back to the laser area, and much to my sales engineer’s surprise, there were no machines running! Oh boy, here we go.
The customer walked our guests around the machine and its associated automation, highlighting his experiences with it, answering questions honestly and openly. The exchange was typical until one of the visiting engineers asked about the elephant in the room: "Why isn’t this machine running right now? It’s 10 a.m. on a Thursday. Is it broken?"
The customer replied, "If I had any more laser WIP off this machine, I wouldn’t know what to do with it. I’ll cut a sheet for you, but we’re just adding to the mountain."
He then walked us in front of several waist-high piles of cut sheets that had yet to be sorted and moved on. The prospect was amazed not only at the stack of metal in front of us, but at how completely calm and at peace the owner was with all of his laser machines turned off at 10 a.m. on a Thursday.
It was an impressive display of fabrication management in the high-power fiber universe. The conflict zone had clearly been entered, and action was promptly taken to keep it from getting worse.
Staying Ahead of the Laser
Once the laser finishes cutting a nest, the battle begins between expectations and reality. Part removal and sorting continues to be a high-friction, high-stress zone. You can easily blame this on the lasers being too fast (they are), but you also shouldn’t ignore two other potential contributors. First, an operation might lack information and foresight into the schedule. Second, the operation optimizes the laser process around cutting and not the real bottleneck of part sorting.
The lack of information and schedule foresight creates a reactive parts sorting environment in which every wrong choice leads to reduced productivity. Think about all the decisions you might make in a day, big or small, and the mental energy they require.
"The lack of information and schedule foresight creates a reactive parts sorting environment in which every wrong choice leads to reduced productivity."
In aviation, pilots fly efficiently and safely by "staying ahead of the airplane." This means knowing or expecting what’s coming, forming a plan, and being ready to execute it. As a pilot moves from smaller, slower planes to larger, faster ones, staying ahead becomes even more important.
You might see where I’m going with this analogy. The process friction in laser part sorting comes from not knowing what to do next, and that shiny new laser that’s cutting six times faster than the old one is just increasing the rate at which these types of decisions need to be made. All the while, you’re accumulating WIP and all the problems and conflicts that come with it. While this can be difficult to quantify on a balance sheet, the challenge certainly has soft costs for all parties involved.
The shops that have chosen to take this challenge head-on are achieving success. For some, this means incorporating an automated parts sorting system. Such automation forces proactive decision-making in the laser department and changes the rules of the laser game in a fundamental way.
A new objective is now present and of utmost priority: optimization for part removal, whether automated or manual. This often will overshadow those three KPIs traditionally used in laser cutting. A commitment to maximizing part-removal ease over all other KPIs will nearly always result in a more productive shift around the laser, lowering labor requirements and overall stress. In this environment, a programmer or scheduler must make a few more proactive decisions, but there should be virtually no decisions made on the shop floor.
Optimizing for part removal even affects processes like material purchasing. The focus should be on obtaining sheet that has little to no coil memory, with stretcher-leveled material being a strong favorite. The margin potential running "cheaper" material usually evaporates in the additional time spent dealing with problems in the sorting area or, even worse, inside the laser machine because of a rogue skeleton.
Preparing a New Part
Today, programmers should look at new parts not from just a cutting strategy and process perspective. Instead, they should consider what it will take to get that part out of the laser department. If there are bend reliefs or other acute corners that operators or end effectors will fight, a program should have relief cuts. Waste destruction strategies should be implemented to ensure slugs are dropping through the grates. Even tabbing certain slugs into place might be called for, since an errant slug or tipped-up hole cutout could interfere with a gripper.
This clearly flies in the face of the nest run-time KPI, but automation is built on stable processes. If a cutting process relies on luck, an automated sorting system will certainly have some bad beats. The equivalent in a manual sorting environment would be "no hammers required."
Nesting Strategy
This is where the real fun starts, and where software helps best with proactive decision-making. When it comes to automated sorting, I often hear people say, "This system is nice and all, but you can’t sort everything." A common reply lately has been, "Well, certainly not with that attitude."
Automated part sorting really does require a mindset change in the entire value stream. Consider a part perceived as too small to be sorted with an automated system. It may be better to group them into a mini-nest or gangtab several parts together that can be picked up and bent with one hit. That turns a negative into a positive. This will certainly affect sheet yield and nest run-time, but they’re small prices to pay for the efficiencies gained downstream. No longer do welders or assemblers say, "I have Part A and Part B of this assembly and not Part C," or, "I have five more XYZ-left than XYZ-right parts at the welding table."
"If the chaos associated with laser-cut part sorting is well managed and properly planned, it’s a good bet that the subsequent operations are going to feel much smoother."
If your shop has robotic welding cells, they’re likely your most profitable work centers and have the highest demands in terms of quality and consistent throughput from cutting and bending. Serving these "internal customer" work centers well can be quite lucrative. Fabrication is not a zero-sum game. Certainly, the value of keeping the welders happy must be more than the pennies picked up from your scrap vendor, or the nickels in extra laser time used to create a stable foundation on which to automate.
In conjunction with nesting, sort planning as well as all decisions regarding those parts occur before a sheet of material is allocated to the job. How the parts are to be oriented, grouped, stacked, and organized is no longer a shop floor function. It is a planned and proactive collection of choices made by humans and assisted by software. All this makes the expected output of the laser department suddenly visible and transparent, which can bring added benefits when parts are moved downstream.
This includes the bending department, where its daily input capability could be cut and ready by 9:30 a.m.—but what are the forming requirements for those cut parts? Most laser programmers could not tell you how many bends are on a nest when they send it to a machine. In this post-IPM world, though, the number of bends really matters.
Cut enough of certain part geometries with a number of bends, and you could easily bury two or three press brakes. Cut enough parts with simple bends or no forming whatsoever, and your brake operators might not have enough parts to bend. This is where manufacturing-execution-system-level scheduling software can be most valuable. At this point, a factory finally begins to become smart and imparts some planning foresight based around accurate models of the manufacturing steps and real-time machine feedback.
The Zen of Modern Manufacturing
If the chaos associated with laser-cut part sorting is well managed and properly planned, it’s a good bet that the subsequent operations are going to feel much smoother. Even the logistics processes now have a chance at being automated with autonomous mobile robots or automated guided vehicles. Remember, every manufacturing step has two logistic steps, getting parts to and from the work center.
Getting away from the old laser management model is a big change, but in the post-IPM world, it becomes a more compelling solution every day. Proactive decision-making just might help you achieve Zen in the art of modern manufacturing.
As published in The Fabricator
By: Brendon DiVincenzo, Head of Solutions for the Americas, Bystronic Inc.