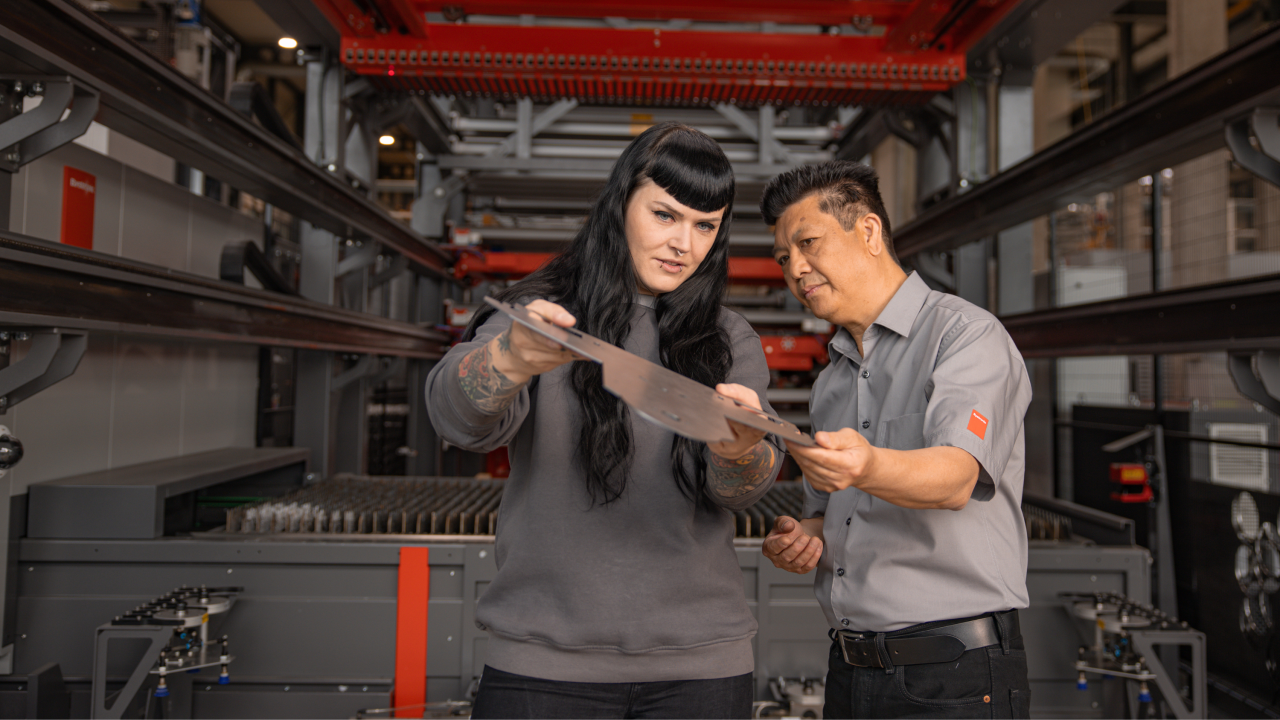
Blog Developing a Comprehensive Laser Cutting Machine Maintenance Strategy
In sheet metal processing, precision and uptime are top priorities. A neglected machine puts your productivity at risk and threatens the quality and consistency of your output. That’s why building a smart, proactive maintenance strategy is one of the most important investments you can make.
This guide walks you through how to build a complete maintenance strategy that protects your equipment investment, minimizes downtime, and guarantees long-term performance.
Why Laser Cutting Maintenance Matters
Laser cutting machines are complex, high-speed systems that rely on precision motion and optical integrity. Without regular attention, even minor issues can necessitate major repairs.
Here’s why ongoing maintenance is essential:
- Consistent Precision: Clean optics and properly aligned motion systems maintain cutting accuracy and part quality.
- Reduced Downtime: Fewer unexpected failures mean fewer interruptions.
- Extended Equipment Life: Regular care helps machines operate longer and reduces the need for early replacement.
- Operator Safety: Well-maintained systems protect your team and help meet regulatory compliance.
- Smarter Production Planning: Fewer interruptions enable more accurate scheduling and on-time delivery.
For Bystronic, maintenance goes beyond a technical checklist. It’s an opportunity to show our customers that we are true partners in their success.
Key Components of a Strong Maintenance Strategy
1. Predictive Maintenance
Predictive maintenance uses real-time monitoring and data analysis to identify signs of wear before they lead to failure. This approach minimizes emergency repairs and allows for smarter, more efficient planning.
With predictive maintenance you benefit from:
- Real-time tracking of machine health
- Maintenance planning based on data
- Fewer surprises and more reliable performance
Pairing predictive tools with preventive checks creates a complete, forward-looking maintenance strategy.
2. Daily Checks and Cleaning
Simple, consistent daily inspections can prevent larger problems down the road.
Make time for these daily tasks:
- Check cables and connections for wear or looseness
- Clean optics and laser bed to prevent buildup
- Inspect coolant levels and air supply quality
Just a few minutes each day can dramatically reduce long-term maintenance needs.
3. Optics Maintenance
The optics system is where precision happens. If the beam path is dirty or misaligned, every cut will suffer.
To keep optics in top shape:
- Clean lenses and protective windows regularly
- Ensure the beam maintains consistent intensity
- Use manufacturer-approved cleaning supplies
A focus on optics is essential because they are central to both cut quality and overall system performance.
4. Attention to Motion Systems
Laser cutters operate under rapid, multidirectional motion. Without regular lubrication and alignment, friction builds and performance drops.
Regular maintenance tasks in this area include:
- Lubricating guideways, belts, and motors
- Monitoring for unusual noise or resistance
- Verifying that all motion components remain aligned
When a machine’s motion systems stay in peak condition, you can expect reliable performance.
5. Cooling System Maintenance
Overheating can quickly damage internal components. Cooling systems must be properly maintained to prevent thermal issues.
Key actions:
- Keep coolant at proper levels
- Clean chiller filters and radiators
- Prepare for seasonal temperature changes with proper coolant additives
6. Slat Condition Checks
Slats often go unnoticed, but they play a key role in part quality and cutting accuracy. Dirty or worn slats compromise performance.
How to manage slat maintenance:
- Replace slats when they start to show wear and tear
- Use a slat cleaner to remove slag buildup and restore surface quality
These simple steps make a big difference in part stability and finished quality.
7. Following a Structured Maintenance Schedule
Organizing maintenance into regular intervals helps prevent important tasks from being overlooked.
Suggested schedule:
- Daily: Inspections, optics cleaning, and coolant checks
- Weekly: Slat cleaning, lubrication, and filter checks
- Monthly: System diagnostics for deeper cleaning
- Annually: Professional servicing, recalibration, and software updates
- Tailored to your production: 360° Customer Advisor inspections to evaluate operator skills, analyze risk components, and assess overall machine condition
A well-maintained machine delivers better output, longer service life, and fewer surprises.
Let ByCare Cover All Your Maintenance Bases
Even with an in-house maintenance routine, professional service adds an extra layer of security. ByCare is Bystronic’s full-service support program, designed to reduce downtime and protect your equipment investment. What sets us apart is our culture of care behind every visit, phone call, and solution.
At Bystronic, we believe maintenance is about more than machine performance. It’s about supporting your team, understanding your production needs, and delivering service with real passion and pride. We’ve built an entire service philosophy around this mindset.
ByCare provides:
- A 30 to 40% drop in service activity during the calendar year for participating customers
- Preventive maintenance through 360° Customer Advisor and Predictive Maintenance through ByCare’s eProactive Service, which both help you detect technical faults early
- A significant decrease in emergency breakdowns
- Service levels tailored to machine usage and production needs
- Discounts on spare parts and consumables
- Certified technicians trained in precision diagnostics
- Operator assessments to minimize user errors, one of the most common causes of downtime
- Simplified production planning due to increased reliability and foresight
- A team driven by passion for quality and customer service
Our people are what make the difference. Maintenance procedures may be similar across the industry, but ByCare is powered by a team that truly cares about your success.
Maximize Uptime with Support from ByCare
Building a laser cutting maintenance strategy prevents problems, improves performance, and extends the life of your investment.
With ByCare, you don’t have to do it alone. Our service experts are ready to support you with passion, precision, and care. Explore ByCare’s service packages today and discover the impact of proactive maintenance.