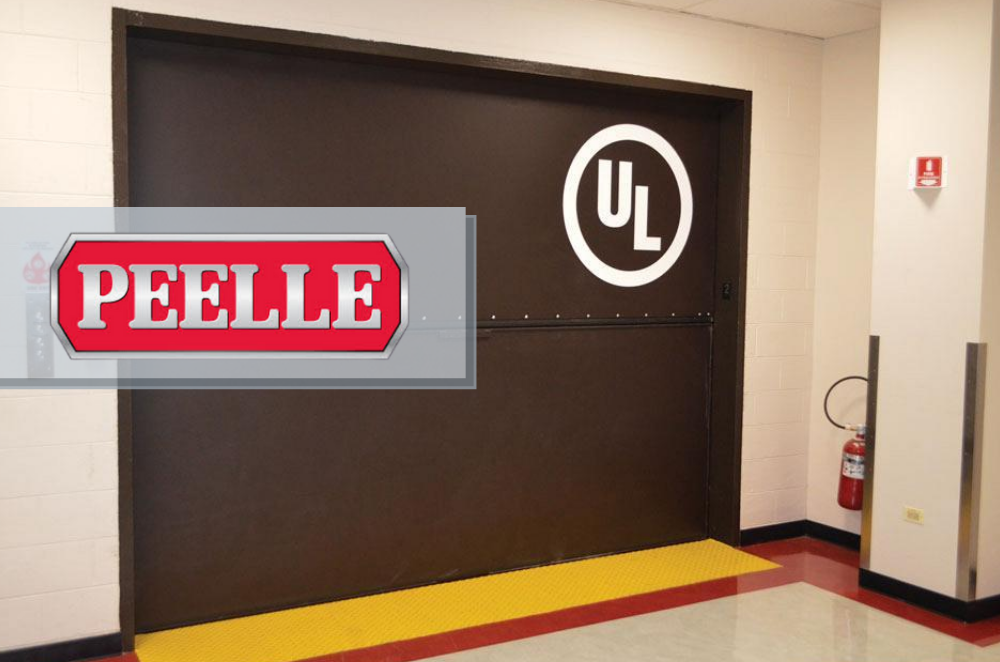
News Opening the door on new opportunities
How does a company grow and become more efficient in a mature market segment? That’s the challenge that Peelle was faced with a few years ago. The company has specialized in the fabrication of freight elevator doors for 113 years. Its bread and butter has been its vertically sliding doors, which save space and make the company’s designs popular anywhere that square footage is at a premium. But a desire to grow the business has pushed the company into the passenger elevator door market. To support that move, Peelle has invested in new laser cutting and press brake technology. These investments have also had an impact on its core products.
Mature Market Management
Peelle’s main product line is a niche one that everyone needs but few companies make.
“Elevator companies like Thyssenkrupp, Schindler, and Kone Elevator are big customers of ours,” said Alex Stobo, vice president of operations at Peelle. “They all concentrate on building elevators for the passenger market. But on big projects like malls, they still have to provide freight elevators, so they subcontract that work out to others. Sometimes they buy the doors straight from us, sometimes the orders for our doors are packaged with that of a consolidator who supplies the whole freight elevator.”
Although the freight elevator market is heavily concentrated in North America, Stobo said the company has made inroads over the past 30 years worldwide.
“Singapore, for instance, has been a big market for us,” he said. “We’ve also done well in the export market in Europe and elsewhere. Anywhere land is scarce, a vertical sliding door on a freight elevator makes a lot of sense.”
It’s a challenge to differentiate yourself in such a niche market, but Peelle has aimed to do so through its R&D support for client projects.
“A lot of the innovation in our market has been driven by safety code changes that require such things as light curtains and touchless reversing edges,” said Stobo. “However, we have introduced other innovations that aren’t required by codes, such as wireless controllers. In the elevator industry, the elevator mechanic is the highest-paid tradesperson. We can save companies time in the field by reducing the wiring requirements. That is why we introduced a wireless controller. Products that can save installation costs have helped us gain market share.”
Each freight elevator door is essentially a custom project, which makes introducing automation into the manufacturing process difficult, if not impossible.
“We go through about 25 projects a week in our factory,” said Stobo. “A project could be anything from replacing a panel on a door to producing a number of doors for a building. Each project is unique. So while we’re curious about automating our welding processes, where much of our labor is concentrated, it doesn’t really make sense for the work we do.”
The variety of work is interesting. As Stobo explained it, the company has job files that go back to the 1920s, so if he gets a call about replacing a door Peelle originally installed in the 1950s, the team can pull up the drawings and understand precisely what is required in that space.
“That’s a real benefit for us,” said Stobo. “It also makes it easy for us to provide replacement parts as necessary.”
Peelle generally has part runs of between one and 10, and the shop runs on lean principles. So while automation isn’t possible on the welding side, material preparation in cutting is an area that naturally lends itself to labor-saving efficiencies.
Laser Upgrades
Peelle bought its first laser with load/unload capabilities about eight years ago.
“That CO2 laser ran around 20 hours a day, usually six days a week,” said Stobo. “Our freight elevator doors are made of mild steel, so we ran everything from 16-gauge up to half-inch material on that machine.”
But just over a year ago, Peelle expanded its production into the passenger elevator door market. The company had decided about two years prior that to grow, it needed to expand its market reach. Last year it outfitted itself with the cutting and bending capacity to make that possible.
Peelle purchased a 6-kW Bystronic fiber laser equipped with a 15-shelf tower, 12 for loading and three for unloading.
“Passenger elevator doors are about 50 per cent stainless steel and 50 per cent galvanized,” said Stobo. “The older machine simply wouldn’t be able to cut the galvanized and would be much too slow on stainless steel. A fibre laser just made sense for the work we were doing.”
The Brampton, Ont.-based facility handles all the manufacturing for this U.S.-based, fifth-generation family business. The 80,000-square-foot facility employs around 100 people, about 60 of which work in the factory running two shifts.
“We started a second shift last year for the new product,” said Stobo. “That’s the first time we’ve ever done that.”
The tower on the laser operates in such a way that after a sheet is cut, it can be placed in any of the three “unload” shelves. Some companies sort these shelves by material or by thickness. Peelle sorts them by project so that each “unload” shelf handles one project. Generally speaking, a project is cut on day one of production; formed on day two; assembled on day three; and painted, loaded, and crated on day four.
The speed of the new machine is quite noticeable to Stobo.
“We cut 100 inches a minute on the CO2 laser, compared to 1,200 inches a minute on the fiber,” he said. “Although we didn’t buy the new machine to replace the old one, we have moved some of our freight elevator door production to the new machine. The older machine was running 95 per cent of the time, so I wanted to cut that back for its longevity.”
The choice of Bystronic was partially a service consideration.
“Our other laser didn’t have service representatives readily available in Canada, and if it were to break down, it was difficult to get sorted in a timely manner,” said Stobo. “We have an older Bystronic press brake and we were always pleased with the service we received.”
Press Brake Accuracy Support
Peelle purchased a 4-metre, 250-ton Bystronic Xpert press brake equipped with its laser angle measuring system (LAMS) at the same time as the laser.
“With all of our work being small batch sizes, setups and corrections are always an issue,” said Stobo. “A lot of time, doing only two parts in one setup, the correction can take twice as long as forming the part. The LAMS technology has really helped us with our throughput. It takes perhaps one second longer to form the part because it is measuring it. But that means we’re not spending as much as 10 minutes correcting a bend. It’s fairly easy to correct a part if it’s underformed, but if it’s overformed, that is another issue.”
Because Peelle has to produce larger panel sections for its doors, the company had the new brake equipped with lift assists.
The two new machines together create opportunities for Peelle to save production times through the first two days of a typical project, making the transition to a broader product offering easier to manage.
Canadian Fabricating & Welding - October 2018For Peelle of West Brampton, ON (Canada)