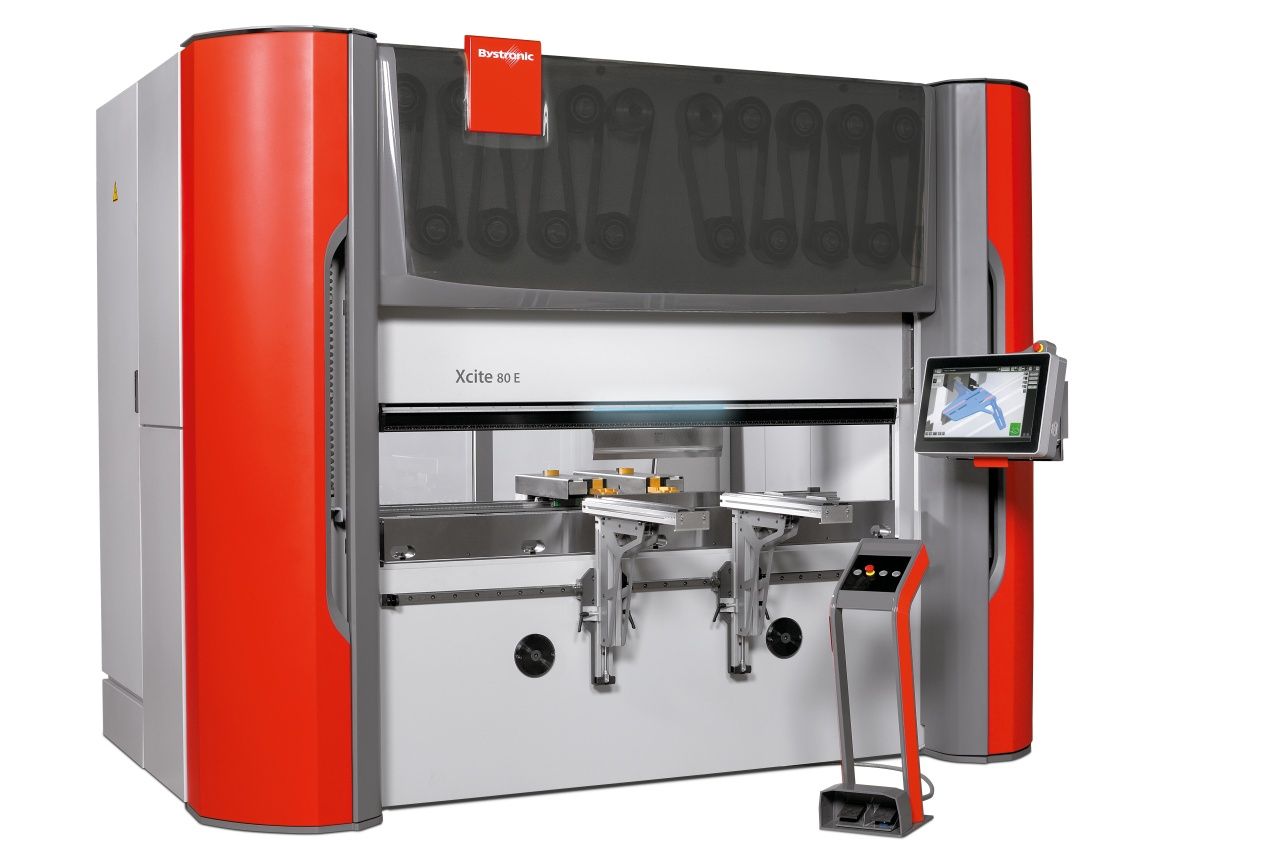
News Keeping safe while bending parts fast on a press brake
Customers want parts right away, and newer laser cutting technology is producing parts quicker than ever before. If a fabricator wants the bending department to keep up, it needs press brakes that can bend parts quickly. Even with the increased bending productivity, however, fabricators don’t have to sacrifice safety.
Historically, most of the developments in press brake technology have been focused on setup times. Changing market requirements forced fabricators to look for more cost-effective ways to address smaller lot sizes. In the 1990s OEMs and their suppliers were no longer interested in carrying large inventory levels through downturns in the economy, and as a result, they put more just-in-time demands on the backs of fabricators.
Today the industry is seeing the proliferation of high-speed fiber laser cutting technology, which also is making another significant impact on the sheet metal industry. Fiber lasers are capable of producing more than twice the parts as the classic industry-standard CO2 laser in the same amount of cutting time. Because of this dramatic change in cutting capabilities, other sheet metal-related fabricating processes inevitably had to adapt as well.
For many fabricators, the next downstream operation after cutting is the bending of those parts on a press brake. However, simply increasing the ram speeds is not the ultimate solution for keeping pace with increasing customer demands and faster laser cutting machines. Increasing overall productivity, without compromising operator safety, is the goal. This is where technology lends a hand.
The Emergence of the Electric Press Brake
Obviously, improving the press drive does have a lot to do with productivity. The newest technology for bending parts faster is the so-called electric press drive (see Figure 1). Electric press drive, or electric press brake, refers to a direct-acting press drive in which turns of the motor are directly related to ram movement.
This usually is accomplished through massive mechanical gear reduction. The ram speeds achievable are higher with this direct-drive technology. Much of the productivity gains are from the ram’s ability to accelerate rapidly; with this scenario, of course, the ram also rapidly decelerates to keep the operator safe.
Electric press brakes are about twice as productive as a conventional hydraulic press brake. This is in step with the production increases associated with the fiber laser cutting technology.
Hybrid hydraulic press brakes often are placed in the same category as electric press brakes because they function much like a direct-acting press drive. This hybrid press brake technology does employ the pump displacement and cylinder diameter ratio to gain mechanical advantage, just like a conventional hydraulic press brake, but the similarity ends there. The hybrid technology’s press drive motor is a servomotor, and the pump sends oil directly into the cylinders. When the pump turns, the ram moves, eliminating the typical reaction time delays associated with flow control valves in hydraulic press brakes.
A Vision of Safety
Light curtains have been used for decades to protect the operator. They create a virtual barrier across the front of the machine. If the operator inadvertently places any part of his body in the guarded zone, the ram is disabled.
Because most of these barriers are based on a single point of physical light interruption, they cannot distinguish between the partially formed blank and any part of the operator. Because of this, the press brake operator often manually mutes the barrier zone or completely shuts off the entire guarding system.
Because of this false security with light curtains, laser- and vision-type guarding systems have been introduced (see Figure 2). These systems are “smarter” than conventional light curtains. For example, they can recognize the difference between a bent flange on a four-sided box and the operator’s hand under the punch. Vision-type systems also tend to allow uninterrupted bending of shorter front flanges too. The laser-type systems act like a limit switch: Break the beam and the ram stops.
An important advantage of vision systems is that they allow the ram to stay in the high approach speed longer before shifting to the slower bending speed. This feature alone reduces the ram cycle time by another 20 percent when compared to traditional hydraulic press brakes.
Some vision systems even resize the safety zone in front of the punch automatically according to ram speed. Each stroke is then optimized even further.
The vision-based systems not only react faster than conventional light guards, but they also tend to have more features because they “see” more information. For example, image systems can be used to verify punch height and punch angle. If the vision safety system does not recognize a tool, the machine stops. This greatly reduces the possibility of shattering improperly installed tooling.
For the complete article, please click here.
By Paul LeTangProduct Manager of Press Brake/ToolingReprinted from The Fabricator - www.thefabricator.comOctober 2014