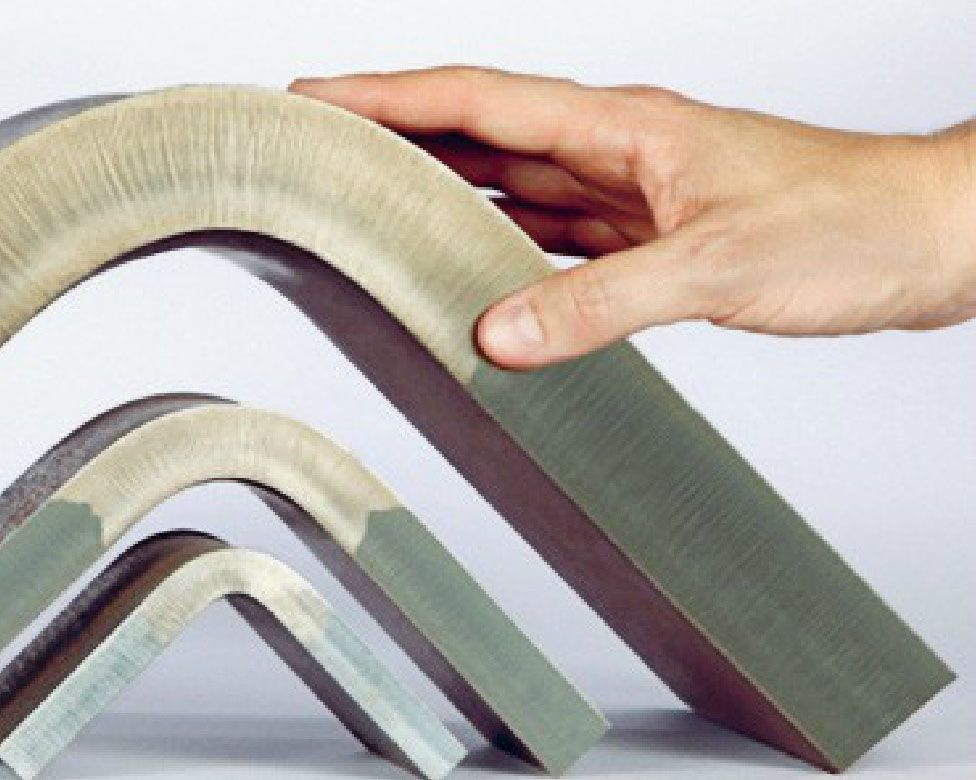
News Bending the Strong Stuff
If you're facing a press brake job with one of the new high-strength steels, one you haven't worked before, brace yourself. It may look simple, but it can be full of surprises. Bystronic's Paul LeTang (aka Dr. Bender) speaks with FAB Shop Magazine Direct's editor, Ed Huntress on bending advanced high-strength steels (AHSS).
Sometimes when we think we have a simple, straightforward story to tell, we lift up the lid and find that it is complex, subtle, and multi-faceted. We know that working with advanced high-strength steels (AHHS) can present surprises. But bending it with a press brake turns out to have more niches and angles than we bargained for.
The dividing line falls somewhere around yield strengths of 100,000 psi. Conventional steels above that degree of strength traditionally haven’t been bent or formed in the high-strength condition; that’s usually heat-treated territory, with forming done in an annealed or normalized state. Sometimes the answer is hot-forming. But the newer AHSS steels developed for automotive structures, which are finding their way into a variety of other applications where lighter weight is desired, are formulated to be relatively ductile and formable. The key word is “relatively.”
We called on one of the most experienced people in the field, Paul LeTang, Product Manager of Press Brake/Tooling for Bystronic, to explain to us how it’s done. Paul has been involved with these steels as they have evolved over decades, and, as AHSS finds its way into more shops, is called upon to help and to solve bending problems. For close to an hour, Paul delivered a detailed list of issues, rapid-fire. Here are the highlights, point-by-point, with apologies for compressing Paul’s in-depth explanations:
Material
- Bending force, springback and the risk of cracking all increase with material strength. Each issue requires individual attention.
- Springback is much greater – often 10 to 25 degrees, as opposed to the 2.5 to 3 degrees typical with mild steel. And springback varies widely with the different types of AHSS.
- Material cleanliness is important. It should be free of rust, shot-blasted, cleaned and oiled.
- Cut edges should be deburred
- Material should be bent at room temperature. Cold material makes problems worse.
- Material has a stronger tendency to crack in both grain directions than mild steel. It should be bent at right angles to the rolling direction (across the “grain”) to minimize cracking.
Tooling
- At the higher levels of springback, U-shaped, versus V-shaped dies may be required.
- Across the grain, the die V-opening requirement will vary somewhat with the material, but it’s in the range of thickness x 7 to thickness x 16. Punch radius will be in the range of thickness x 1.5 to thickness x 8.
- Bending with the grain, die V-opening should be from thickness x 9 to thickness x 18. Punch radius will be from thickness x 2 to thickness x 8.
- The die shoulder radius should be at least one half the plate thicknesses, and it should be hardened and polished. The die shoulder radii must be cleaned and lubricated before each use.
- It’s less likely to crack if ram speeds are reduced. These materials are strain-rate sensitive; they needs time to flow. In problem cases, we tell the user to slow down to approximately 10% of full speed, and the problem goes away.
The last point raises questions about machines, which are under vastly greater loads when bending AHSS. Paul had more comments about that later.
Several of the bullet-point issues above beg for more discussion. The grain-direction issue, for example, suggests that nesting patterns are a bigger issue with AHSS. “Because of the big differences in radii that you can achieve with the grain versus across it, and because you’re likely to be bending radii that are closer to the limits with high-strength steel, you can’t just fit parts to make an efficient nesting pattern,” Paul says. “If you can design a part such that the tightest radius is within allowable limits for the bending direction parallel to the grain, you’ve solved that problem. But some of our customers’ problems bending these materials stem from not taking this into account.”
“As material strength goes up, it becomes more brittle, despite efforts to achieve ductility with the newer grades. As it becomes more brittle, of course, it’s more inclined to crack. But the relationship is not linear. The relationship to bending radius, for example, is exponential. The problems grow fast as strength of material increases.”
“As an aside, some applications are performed hot. There is the hot-forming automotive parts business [such as extreme-strength door pillars made with boron-containing steel grades – ed.] done with big sheets, big ovens, and robotics. But there are possibilities for smaller operations to hot-form smaller parts with less elaborate equipment. As a rule of thumb, the forces, springback and radii can be cut in half when bending hot high-strength steel.”
“Higher-strength steel wants to yield in a single point, not in a nice smooth radius. So the basis for punch selection, and of course for die selection, are different. The tool radii have to be much larger and you have to be aware of that tendency for the material to yield locally.”
“Normally, air bending mild steel, your V-die is eight times metal thickness. That's the normal rule. When you get into the high tensile material, the rule gets a little more vague. There is a range of limits that varies with the specific material. When you buy steel form the supplier, you can request a spec sheet now with that material and it will be guaranteed that this material complies with these specs. And a lot of times, on the spec sheet, it has your minimum radius, your V-opening selection, your minimum yield; a lot of the details are on that technical spec sheet. It can be a big help.”
“If you want to bend a part to 90 degrees, you better have very acute angle dies, because you're going to have a range of 10 to 25 degrees springback. In contrast, for mild steel, you could spring 2.5 degrees. So typically, if I want to make a 90 degree air bend, I'll bring the ram down to 87.5, and you release the part and it springs open 2.5 degrees. Not with high-strength steel."
“With high-strength steel, the range of springback is so wide that it can result in a lot of trials to get it right. There are technical solutions that minimize them. We offer two different ones at Bystronic; other manufacturers have their own. They really come into their own with these high-strength steels.”
At this level, we have tried to boil Paul LeTang’s extensive knowledge into a bullet list of things to look for and to question. He delved deeper into die design and operation for AHSS, which is a subject that will be treated in a subsequent article. Likewise, systems for minimizing testing for springback, and the machine tools themselves.But there are a couple of general machine comments that are essential to a preliminary evaluation. Many press brakes are going to be very limited in the size and thickness of AHSS parts they can handle. Bystronic builds 1,000-ton press brakes, and the dynamic loads are extreme.
“Machines have a lot of flex or deflection. You're bending steel with steel but I always think of it like you're bending rubber with rubber. The machine flexes so when your tensile strength goes up, your press brake deflection goes up. We have a solution that's commonly applied with high tensile material. We call it a dynamic crowning system. You’ve heard us talk about it before, but it becomes more important in the high tensile range. What it does is measure the machine flex and compensate in-process."
“It does this on the fly and it does it per-bend, because what you see a lot with the high tensile is the part shapes, and thickness, and length change often. We have two parts that are twenty feet long, the next part is three feet long, the next part is one quarter, the next part is one half, so the material is constantly changing from job to job."
“We do two things. We readjust the crowning table hydraulically. There are cylinders in the table that we pump up to compensate for the ram and bed deflection. And then we also compensate with the two main ram cylinders for the side-housing deflection. In press brakes you have two weak points. You have the ram and the bed that are weaker in the middle, and then you have your two side frames that are a C shape. You have to compensate for the deflections when you’re working with high-strength material.”
And there is more. It sounded so simple at first: higher strength material, more force. We’ll have more to say about the implications for tooling, and machine limitations, in future issues.
Reprinted with permission from the August 2014 issue of FAB Shop Magazine Direct.By Ed Huntress, editor, FAB Shop Magazine Direct - www.fmsdirect.com
With Paul LeTang, Product Manager of Press Brake/Tooling, Bystronic Inc.