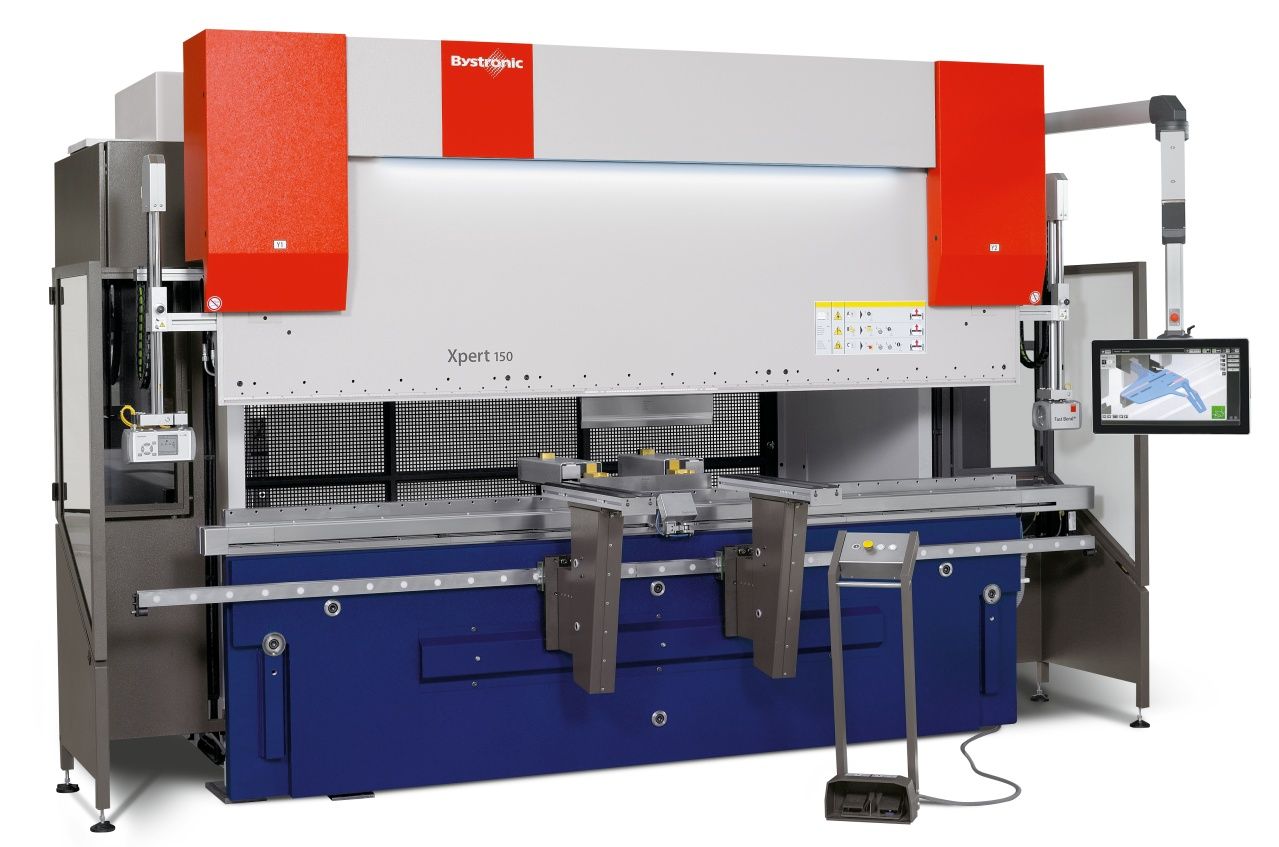
News Bent on Success
Structural steel culvert fabricator invests in a robotic bending cell
A Canadian fabricator is redefining the structural steel culvert industry with a multi-million dollar investment in a robotic bending and material handling cell.
In an industry dominated by manual fabrication processes, Canada Culvert, Cambridge, ON, is forging ahead with a fully automated bending operation measuring 15 by 30 m (50 by 100 ft) comprised of two Bystronic Xpert press brakes, 800 ton and 500 ton, and three Titan robots from KUKA Robotics.
"To the best of our knowledge and in conversations we've had with suppliers in Europe and in Canada, this is the first system of its kind in the world," says Stan Resler, national operations manager for Canada Culvert. "The executive team of our parent company, WGI, have been very supportive and understand that we have to change the way we do business if we're going to grow in the future."
Canada Culvert is part of Westman Group Inc. (WGI), which owns several other manufacturing businesses including Meridian Manufacturing, Behlen Industries, Westman Steel and Frontier Laser.
When Lyle Button joined Canada Culvert six years ago as production manager, one of the projects the 36-year culvert manufacturing veteran was involved in was to research the best fabrication process for a new structural plate corrugated steel pipe line the company planned to manufacture. Everyone in the company, from shop floor workers to the executive team at Canada Culvert and WGI brought their ideas to the table.
"You can roll form culverts but when you get into larger size sheets measuring 12-ft wide, the roll former would have to be massive. So it wasn't an option for us," explains Button.
The large culverts are fabricated in 13 different widths ranging from 850 mm (3 m) to 4028 mm (13 ft) and in three different lengths 1219 mm (4 ft), 3048 mm (10 ft) and 3658 mm (12 ft).
The company considered automated feed tables for material handling, but ruled that out as well because it would limit the company from introducing other products onto the line. It also considered different types of press brakes, including used ones from a variety of press brake suppliers.
In 2012, it decided on an automated bending cell. It took another year to put the system together with the help of robotic integrator, New Age Robotics, Ayr, ON.
One challenging aspect of programming the robotic bending cell was how the robot handled and supported the corrugated culvert as the radius work was being perfromed on the second Bystronic press brake.
Finding the right equipment
"We found that the Bystronic presses had what we needed," explains Button. "These are highly accurate presses that maintain their accuracy in a closed loop robotic bending cell. Now we put the blanks in at one end using a forklift--the only thing done manually--and the culvert comes out at the other end completely finished and 100 per cent accurate."
While Button and the team liked the accuracy the Bystronic press brakes offered, what impressed them most was the hydraulic dynamic crowing.
"A press brake typically distorts your rams and bolsters distort from deflection because of the force of the cylinders coming down. Bystronic has designed its presses so that the cylinders are in the lower bed to counteract the bending of the ram and the bolster, which makes for a highly accurate press."
The cell has been in operation for eight months, but Button says the team continues to optimize the system.
"Programming has been the biggest hurdle but we continue to optimize it. We're planning to add other products to the cell and it has been designed around future expansion."
By Mary Scianna, EditorShop Metalworking TechnologyJune 2014