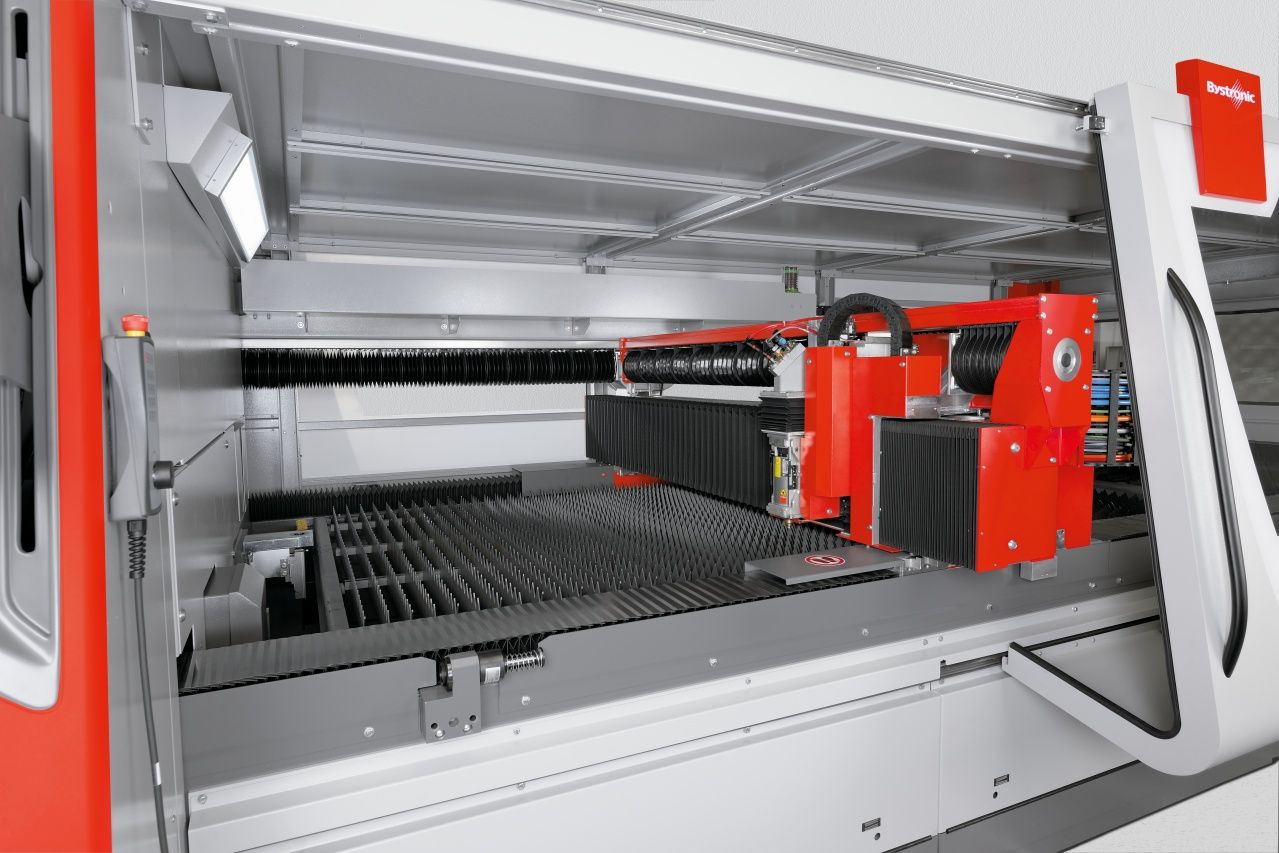
News Tech Upgrades Add Efficiencies to ADAM Integrated Shop Floor
ADAM Integrated Industries Inc. was launched seven years ago by the McMaster and Meikle families in Salmon Arm, B.C. It is a full-service metal fabrication and manufacturing shop serving a broad industry base. And when they say full service, that’s by no means an understatement. The services include design, 5-axis waterjet cutting, computer-aided forming, laser cutting, full welding services, as well as abrasive blasting and electrostatic powder coating. The company also considers shipping and packaging an important part of the process, so customers get delivery the way they want it.
“The big difference between us and a lot of shops in western Canada is that we handle everything from design to finishing, so we have a lot more control over the manufacturing process,” says ADAM Integrated President Colin McMaster. “Not a lot of shops offer the design services we do either. We are often able to work with a client’s idea of a product and take it to the next level.
“We can also work with them to modify the manufacturing processes to take advantage of the technology we have in-house,” McMaster continues. “A lot of people are accustomed to using plasma cutting here, so their parts are often spec’d out to that standard. Because we have a waterjet table and lasers, we can give them a greater level of accuracy. For instance, we’re able to do lots of tabbing so that basically the sheets all tab together. By leveraging the technology, we can provide a better part.”
ADAM Integrated prides itself on, and advertises itself as a business that focuses on quality control processes and high efficiency production techniques – essentially letting its clients know that they can get quality parts fast through their shop. The company’s location serves as a selling point as well – ideally suited for shipments to Calgary, Edmonton, Vancouver and the B.C. interior. The company works primarily in aluminum, stainless steel and mild steel. They serve a broad client base, including the oil & gas industry, and complex acoustical building parts.
“Given that, in general, the size of orders is getting smaller because no one wants inventory, the transaction cost becomes a significant part of the overall cost,” notes McMaster. “We are in the process of implementing E2 software to assist in the flow of paperwork and real time data capture. Along with this, we are implementing BySoft 7 to control both our laser and press brake. We see the value in having one supplier for both processes and software, as we need to shorten the time from drawing to completed part and reduce, or event eliminate, the need to do test pieces to get bend allowances and brake tooling collisions addressed.”
The E2 Shop System is manufacturing software designed to give a user optimal control of their shop floor. It brings all of a business's operations into one manufacturing software solution - from estimating to accounting and every business function in between. It includes an order entry system, an inventory manager, a scheduling whiteboard, and a shipping program that integrates with UPS World ship, Fed Ex and other carriers so that customers can track their parts from dock to dock.
BySoft 7 is modular CAD/CAM software with 2D and 3D CAD as well as extensive functions for scheduling and monitoring manufacturing processes developed by Bystronic. With the program, users can quickly design tailored parts and create cutting plans and bending programs with the push of a button. Furthermore, manufacturing processes can be scheduled and monitored efficiently using it, thus maintaining an overview and finishing jobs quickly and economically.
Existing drawings and models can be input, edited, and processed on the system. Users can see a reduction in parts costs, because BySoft 7 automatically nests parts in the most effective manner. Raw materials are used in their entirety. This also applies to the processing of tubes and profiles.
ADAM Integrated has 32,000 square feet of production space, 4,000 square feet of office space, and a crew of about 57. And the company is constantly introducing new technology to improve efficiencies and productivity. For instance, the company will introduce two new lasers and a new press brake this fall.
“We bought our first Bystronic laser a year and a half ago,” says McMaster. “We’ve decided to trade that laser in and replace it with the new 5 x 10 table ByAutonom with sheet loading capabilities and a 6 x 12 table BySprint Pro. The ByAutonom will be set up with a two-pallet system, each of which can hold about 5,000 lbs of plate – it’s really the first level of automation available. The new press brake we are bringing in is an Xpert 320, with a bending length of 4 m, and a tonnage of 360 US Ton.”
The ByAutonom 3015 is the newest CO2 laser system from Bystronic. It has a high degree of autonomy thanks to collision detection, a lens-cassette changer, nozzle changer, and automatic nozzle alignment. This reduces non-productive time and increases process reliability. Fewer operator interventions are required, thus freeing up time to concentrate on planning and control. With its Maintenance Messenger system, the machine control notifies the operator when the machine and laser source require maintenance. With its Condition Messenger, the machine control continually collects data on the condition of the machine components. It informs the operator if a component requires checking.
The decision to trade in one laser for two was a function of floor layout and technology. Bystronic gave the company fairly reasonable terms to update to the latest technology, and the ByAutonom’s longer, more linear layout worked well next to the squarer design of the BySprint Pro in ADAM Integrated’s facility. Technologically speaking, adding the two-pallet changer increases the company’s efficiency on the one laser, and the nozzle changing and automatic nozzle alignment was a valuable upgrade from the former model laser they had been running.
McMaster is very pleased with the choice of upgrades. “We’ll probably have a significant advantage over local shops even if they are employing lasers,” says McMaster. “The ByAutonom, with its first level of automation, should give us a competitive edge for quite a while.
ADAM is also introducing a large robotic welding cell in November. The Lincoln Automation system includes a large robot on a slide rail. It has two individual rotary welding bays and each one can handle up to a 102 in. swing and a 140 in. long part – basically a 51 in. radius.
“There are a number of products that will likely move to the cell,” says McMaster. “There wasn’t one part that convinced us that this would be a good investment, but we knew it would be a competitive advantage. It’s kind of a chicken-and-egg type problem. You have to have the competency using this type of system before you can go and sell it as part of your business. We have the confidence in ourselves that we can master this and make it a valuable addition to our business.”
The robotic cell has both a 2D camera and a 3D laser sensor on it, so basically as long as a part can fit in that bay, the system can weld about anything.
“Such a large robotic welder may be overkill for some parts, but it’s always easy to use a big machine to do small parts. But you can’t work on big parts with a small machine,” says McMaster. With many jobs for the company coming from the oil & gas sector, investing in a larger robot makes ample sense.
McMaster and other team members were heading to Toronto for training on the Lincoln system so they will be ready for delivery in November. As McMaster sees it, these investments just prepare the company for the future – a future that will undoubtedly demand the versatility these investments add to their shop floor.
To balance out its job shop work, ADAM Integrated also produces its own industrial acoustical noise control systems, which represents about 30 percent of the company’s production. To learn more about the company, visit their website at www.adamintegrated.ca. To learn more about Bystronic’s product offerings, visit www.bystronicusa.com.
By Rob ColmanMP&P (Metalworking Production & Purchasing)February/March 2014, Volume 41, Number 1