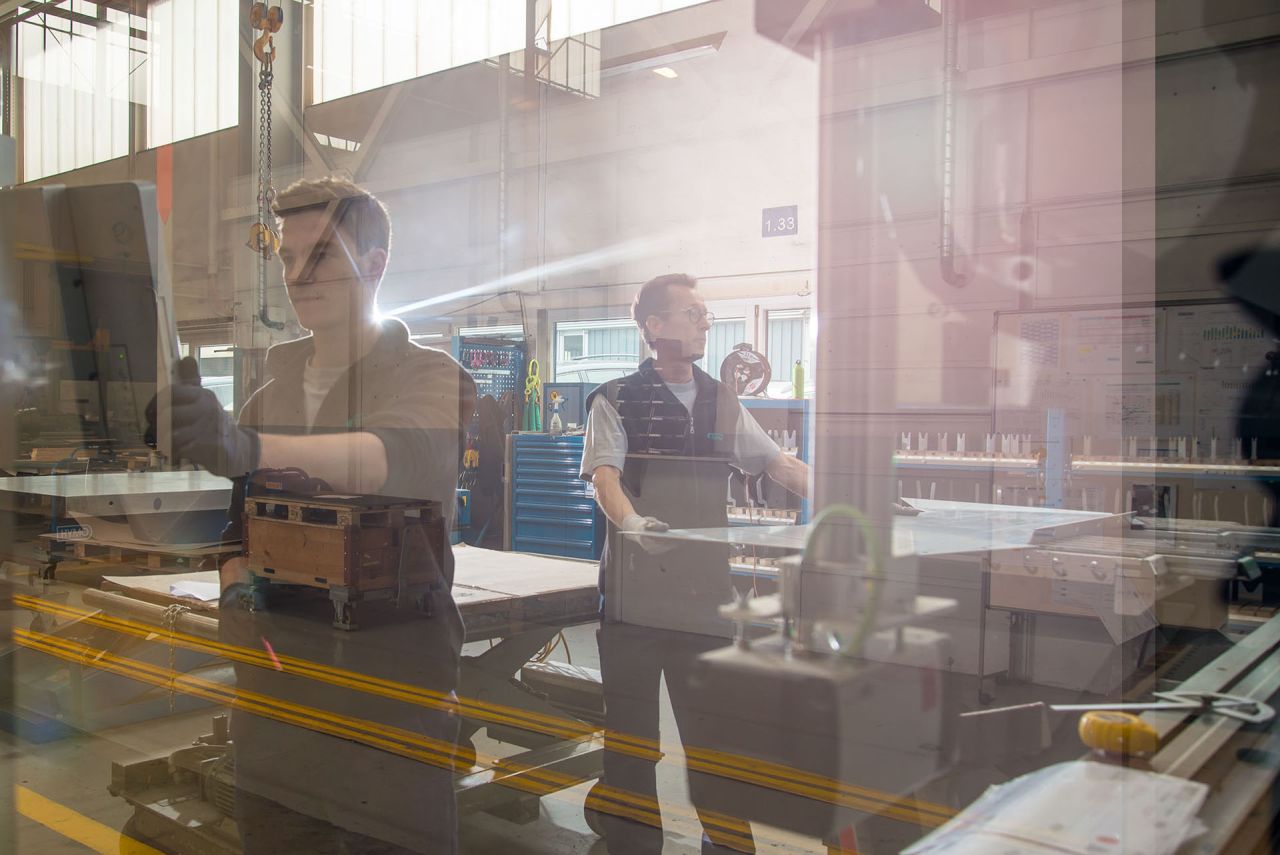
News The Superuser Generation
The Bühler Group's Appenzell plant is creating jobs for digital natives. This is hardly surprising: Founded in 1860, the family-owned company has always distinguished itself by staying ahead of its competitors in terms of innovation and by conquering new markets with innovative products. The Bühler Group is the market leader in many sectors: All around the globe, their technologies are used for food processing in mills, chocolate factories, or breweries. Every day, their solutions ensure a healthy and safe diet for two billion people and help provide mobility to one billion people. Recently, they also successfully opened up new fields of technology, for example with equipment for waffle production and with battery manufacturing solutions.
The Bühler Group is driving innovation ahead not only with new products, but also with the digitalization of its production processes. Since the beginning of 2018, when the entire sheet metal processing was completely modernized, the Appenzell plant is one of the Group’s flagship business locations. While the company’s main plant in the nearby municipality of Uzwil concentrates on series production, special parts are manufactured in Appenzell, for example spare parts for older models that are no longer produced in series. As a result, the 80 employees are used to a high degree of flexibility and were able to quickly familiarize themselves with the new bending machines and the automated storage, cutting, and sorting system.
All-round automation for cutting
“My job used to be physically very challenging,” Maurus Koller says. His work frequently involved welding, his job was tough. “Now mental tasks are more important.” The 30-year-old plant and equipment technician is the "superuser" for the new laser cutting and sorting system at the Bühler plant in Appenzell. The new tool in Koller's toolbox: the mouse. Using drag-and-drop on the screen, he distributes sheet metal parts from the ByStar Fiber 4020 laser cutting system onto the awaiting pallets. The automatic handling and sorting system executes his instructions. “Here I see first-hand what I am learning during my studies", says Koller, who is continuing his education as a mechanical engineering technician, referring here to the digitalization of the industry.
For the digitalization of the cutting processes, Bystronic opted for an individually customized end-to-end solution. The key feature: the combination of Bystronic technology with third-party machines. For example, the handling and sorting system was supplied by the Bystronic subsidiary FMG. It functions fully automatically: A robotic arm uses vacuum suction cups to pull metal sheets from the extended cassettes of the FMG high-bay storage system, which had already been installed a few years previously.
An inkjet printer that was integrated into the system especially for the Bühler Group marks the planned sheet metal parts on the metal sheet with a bar code before they are cut. This will enable the production documentation to be digitalized. Currently, each sheet metal part is accompanied through the production process by an order sheet. In future, employees will be able to register processing steps directly on the part simply by scanning the bar code.
For parts that will be screwed together later, a portal on the handling and sorting system, which was also custom-made for Bühler, cuts threads before the parts are cut. During the subsequent cutting process, the laser cutting system takes the resulting bending allowances into account. After cutting, the system places the sheet metal parts on the designated pallets, which are then sent to the next work stations. The handling portal disposes of the residual sheets in a skip. After the laser, a deburring machine from Ernst removes any irregularities on the edges of the sheet metal that occur during cutting – a job that Bühler employees used to perform manually.