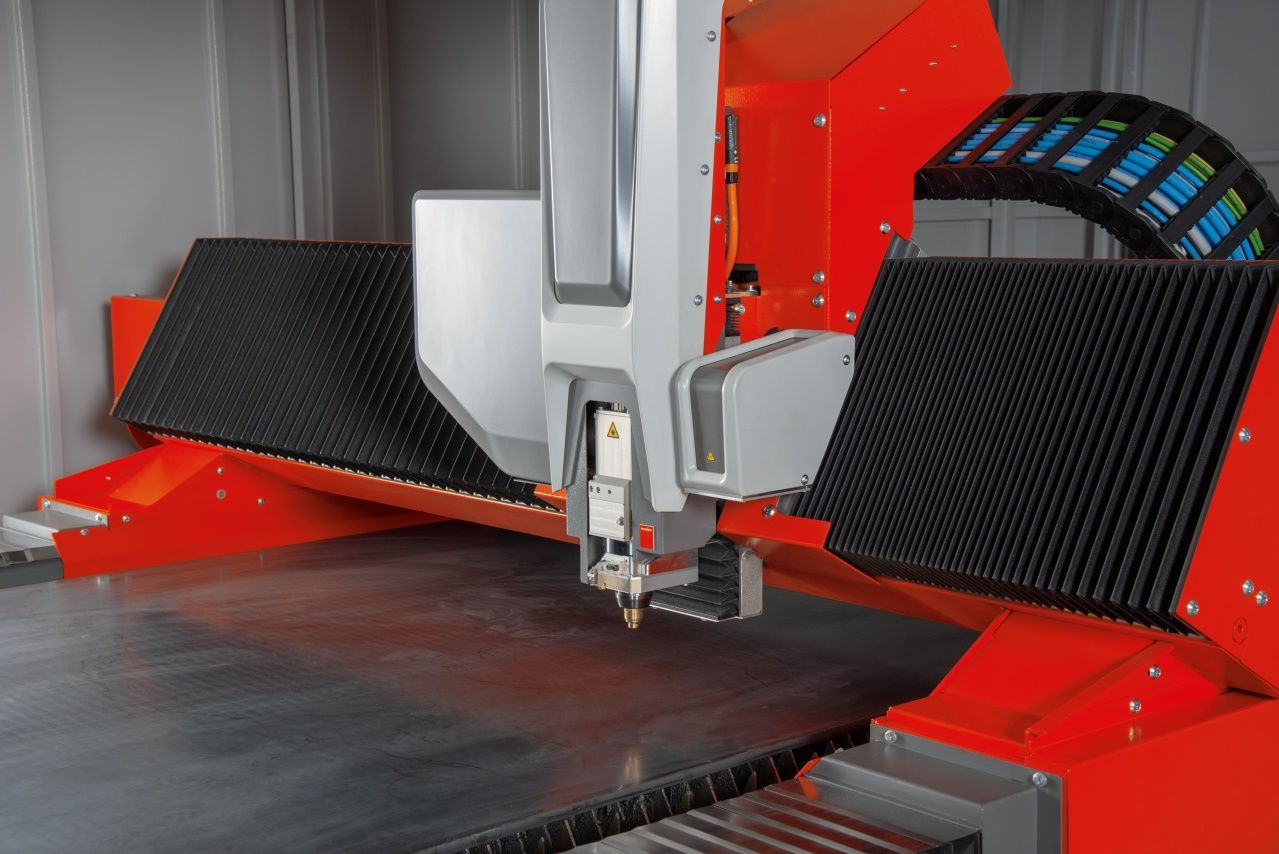
News Powering up your laser capabilities
High-powered fiber lasers can change how your shop operates, but power is only one consideration.
In less than 10 years fiber laser technology has matured to such an extent that it is now possible to equip your shop with a 12-kW fiber laser that can effectively cut both thin and thick material incredibly fast and with minimal to no post-processing required.
Inevitably, as power capabilities increase, shop owners have to consider the value proposition. Is a 12 kW the best value for current and projected needs? As with so many machine investments, the answer depends on your product mix and reasonable growth projections over the next three to five years. If you calculate that a machine you were considering for purchased will be tasked to go beyond its capacity in a shorter amount of time than that, a higher-powered laser will make more sense.
Beyond that, it’s important to understand the other factors than can affect productivity and flexibility, including beam management, consumables, and automation options.
Shift to Fiber
Fiber laser technology was adapted quickly when it entered the market. The advantages compared to its CO2 forerunner technology, particularly for thin materials, were immediately obvious. In thin materials, processing times were shorter and power consumption was lower. In terms of maintenance, there were no lenses to clean or beam alignments to be concerned about. The benefits from the higher throughput of the fiber laser combined with a lower overall cost per part could not be ignored.
The power density of the fiber laser beam is far greater than a CO2. In practical terms, this meant that it could cut faster using a very fine, very powerful beam on thin material. The fine focus of the beam, however, made cutting in thicker material problematic. Although cutting thicker material is possible on the laser, the fine beam required the laser to go slower to ensure the molten cut material was blown away from the part. The result was a part that might require deburring and edge finishing.
However, if your shop is shifting from a CO2 laser, deburring and edge finishing may not be your first concern – again, depending on your product mix. If you are replacing a 6-kW CO2 laser with a 6-kW fiber laser, it’s possible to almost double your production capacity. Cutting with nitrogen, a fiber laser will achieve a clean finish on parts up to ¼ in. thick that will require little to no edge processing before bending.
Increased Depth: 8 and 10 kW
With the introduction of 8- and 10-kW fiber lasers, the range of materials you can cut using nitrogen increases. The “mid-thick” range – anything from 11 ga. up to ½ in. – is the bell curve for these higher-wattage machines. With these machines you can get the most volume out of the same floor space. The 10 kW is popular because of its combination of power and speed. If 80 per cent of your production runs within this range, this is the ideal power level.
Speed Advantage Increase: 12 kW
With a 12-kw laser, it's possible to expect a 20% increase in speed beyond that realized with a 10-kw machine.This technology is being used in a variety of industries, including agricultural, where a lot of parts are made in ½-in. or thicker steel.
Speed
Speed is not just a function of kilowatts, of course. It’s important to ensure that any machine you invest in can take full advantage of the power of the laser to which it is paired.
The rate at which a machine can decelerate into and accelerate out of corners and tight arcs can have a significant effect on cycle time. Visiting a supplier for a proper demonstration of your parts in process on a laser is critical during the purchasing process.
Beam Management
Once you go beyond the “sweet spot” of each of these machines using nitrogen to cut, it’s necessary to switch over to oxygen cutting. Typically, oxygen creates slight discoloration and a somewhat rougher edge finish on a part.
However, machine tool builders have now developed beam manipulation technologies that make it possible to widen the laser beam, such that it’s at an ideal width somewhere between what you see in a fiber laser and a CO2 laser. This allows you to maintain a relatively high-speed cut using the fiber laser while still getting a finish that requires little to no edge processing. New beam-shaping technology allows for an ideal adjustment of the laser beam profile to cut thick steel plate with diverse material characteristics. In steel materials up to 1.125 in., the new function raises the quality of the cut surface and increases the cutting speed by up to 20 per cent when cutting with oxygen.
The cutting head is the core element for a stable cutting process and consistent high part quality. This applies all the more with increasing laser power, which must be delivered to the cutting material precisely and reliably.
A key element in cutting head design is ensuring that there is no possibility of contact with cut features during the cutting process. It’s also important that the head be protected from contamination occurring from cutting dust, for example.
Cooling of the cutting head ensures consistent cutting performance, particularly for long-lasting cutting operations with high laser power. Be sure to understand how this is managed in any machine you consider. Is there a specific cooling mechanism to look for: the entire cutting head, just the focusing optics, or both?
Other Efficiencies
Electrical consumption does increase when you shift from, say, a 4-kW fiber laser to an 8- or 10-kW model, but provided there is a steady throughput of parts, cost per part can drop by as much as a third.
There is no question that with increased cutting speed and thickness, more nitrogen is consumed in the process. However, consumable investments can have an impact on that too. For instance at Bystronic a nozzle has been developed that funnels the assist gas in such a way that it more efficiently gets through the material and blows the molten material away. This makes the company’s 10 kW and 12 kW machines about equal in their use of nitrogen. Whatever system you are looking at, ask suppliers how consumables can augment the machine’s performance.
Space Constraints
In some ways a fiber laser is only as powerful as the throughput that is possible in the shop. Without automation that can keep up with its productivity, a 12-kW machine can’t be used to its full potential. With any investment it’s important to consider how much additional space you might have for various load/unload and sorting options. Will a new machine be added to an existing tower? How much square footage and what storage options do you have to work with? The options are flexible and needn’t be made all at once, but having a vision for how you plan to grow will help any supplier work with you to get the right fit.
A range of automation systems can help guarantee maximum machine utilization and process reliability even during unmanned operation.
The expression “If you build it, they will come” suits investments in laser cutting technology. In time a 12-kW fiber will draw more customers to your shop. With a higher wattage, the machine generates greater capacity because of its higher throughput. This greater capacity provides the opportunity for that additional business and increased revenue.
But to determine which laser is best for your five-year plan, consider where the majority of your production is focused right now and how beam shaping and automation might improve the output of that focus while also expanding your shop’s reach. Most important, ensure you understand how you can run the machine you invest in as efficiently as possible to get the most value from it.
Reprinted from: Canadian Fabricating and Welding, July 2020By: Nikki Amico, Project Management-Solution Center Expert, Bystronic, Inc.